Demonstrating Fletcher Building values with Winstone Wallboards
At FletcherTech, we talk a lot about Fletcher Building values, and demonstrating our ‘values in action’ – but what does that look like?
One excellent example of how the FletcherTech team embodies Fletcher Building values Better Together and Customer Leading is through the positive work we’ve done with our customer, Winstone Wallboards , which is a business owned by Fletcher Building. Winstone Wallboards is renowned for making GIB plasterboard, as well as the jointing and finishing products used to put the plasterboard on the wall. This partnership highlights the collaborative spirit and customer-centric approach that Fletcher Building strives to uphold.
In 2020, Winstone Wallboards realized they needed a larger manufacturing space to meet growing demand and improve operational efficiency. This led to the decision to move their plant from Penrose, Auckland to Tauriko, Tauranga. The move was a significant undertaking, involving the relocation of not just manufacturing equipment but also the establishment of new office spaces. The new site required a comprehensive fit-out, including everything from telephones and printers to video conferencing rooms and service providers. This was a massive logistical challenge that required meticulous planning and execution.
The FletcherTech team played a crucial role in this transition. Our team was responsible for ensuring that the technological infrastructure at the new site was state-of-the-art and met all the operational needs of Winstone Wallboards. This involved setting up advanced communication systems, integrating new software solutions, and ensuring that all hardware was installed and functioning correctly. The goal was to create a seamless transition that would allow Winstone Wallboards to continue their operations without any significant disruptions.
By 2023, the new plant in Tauriko was ready to be used. However, before the new Winstone Wallboards manufacturing site in Tauriko was considered fully operational, the Winstone Wallboards commissioning team had to test the plant. This testing phase was critical to ensure that all systems were functioning as expected and that the new site could handle the production demands. The commissioning team worked tirelessly to identify and resolve any issues, ensuring that the plant was ready for full-scale operations.
The collaboration between FletcherTech and Winstone Wallboards during this period was a testament to the value of working Better Together. The teams from both companies worked closely, sharing knowledge and expertise to overcome challenges and achieve common goals. This collaborative approach not only ensured the success of the project but also strengthened the relationship between the two companies.
Customer Leading is another core value that was exemplified during this project. FletcherTech's commitment to understanding and meeting the needs of Winstone Wallboards was evident throughout the process. From the initial planning stages to the final testing phase, our team was focused on delivering solutions that would enhance the operational efficiency and productivity of Winstone Wallboards. This customer-centric approach ensured that the new site was equipped with the latest technology and was capable of supporting the company's growth and expansion plans.
In conclusion, the successful relocation of the Winstone Wallboards manufacturing plant from Penrose to Tauriko is a shining example of how the FletcherTech team embodies the values of Better Together and Customer Leading. Through close collaboration and a customer-centric approach, we were able to help deliver a state-of-the-art facility that meets the needs of Winstone Wallboards and supports their growth. It is a testament to the power of working together and putting the customer at the heart of everything we do.
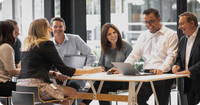
To ensure they were ready and cleared as competent, the commissioning team first went through rigorous training and certification designed and overseen by the tech team. Between January and April this year, Winstone Wallboards logged over 2,000 hours of training.
Cornerstone was set up as the learning management system (LMS). Cornerstone is used as a digital training tool within Fletcher Building corporate but setting it up for a manufacturing site was not without its complexities.
The FletcherTech team had to make accommodations as many frontline workers or people who work on-site rather than in an office, did not have a desktop. Therefore, the tech team provided frontline workers access via an onboarding process. As frontline workers were onboarded, they were provided licenses, logins, passwords, and access to kiosks to use to get into Cornerstone.
Health and Safety is Fletcher’s Building’s top priority, and this training was deliberately designed to be simple, straightforward, and easily accessible for frontline workers in the same way.
The training set up for Winstone Wallboards Tauriko was so effective that the FletcherTech team is now working on implementing similar systems for the rest of Fletcher Building’s building products division, as well as PlaceMakers and Fletcher Building Australia.